 |
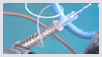 |
|
 |
|
 |
Dyneon Polymer Additives offer improved
mar resistance, a reduced coefficient of friction
and improved non-stick properties when incorporated
into resins for injection molded parts.
They are typically added to thermoplastic
and engineering resins used in the production
of plastic parts such as bearings, joints
and guides that are subjected to sliding friction.
Polymer additives also increase chemical and
temperature resistance as well as wear and
scuff resistance. |
|
|
|
|
POM (Polyacetal) |
Polyamide 6.6 |
PBT (Polyester) |
PU (Polyurethane) |
PP (Polypropylene) |
Polyamide 6 |
Polycarbonate |
PPS (Polyphenylene
Sulfide) |
PE (Polyethylene) |
|
|
|
|
 |
Friction reduction |
Tear resistance |
Viscosity increase |
Wear resistance |
Scuff resistance |
Non-stick properties |
|
|
|
Properties |
Unit |
Test
method |
PA
5951 |
PA5952 |
PA5953 |
Average
Particle size |
§ |
Laser
Diffraction |
6 |
15 |
8 |
Bulk
density |
g
/ l |
ASTM
D 4895 |
350 |
450 |
400 |
Specific
surface area BET |
§³/g |
DIN
66131
DIN 66132 |
10 |
2 |
2 |
Food
contact use |
|
FDA©ö
EU©÷ |
Yes
Yes |
No
No |
No
Yes |
|
|
©ö : These
products comply with 21 CFR 177.1550 and may
be used as articles or components of articles
intended to contact food subject to the provisions,
including specifications, conditions of use,
and limitations, if any, in this regulation.
Dyneon makes no recommendation about the suitability
of these products in the user's intended application.
It is user's responsibility to determine whether
its use of Dyneon products in a particular
application is suitable and will comply with
applicable laws and regulations.
©÷ : It
is hereby certified that monomers used for
the production of the above-mentioned product
supplied by Dyneon are listed in the EU-Directives
90/128/EEC, 92/39/EEC, 03/9 EEC, 95/3/EC,96/11/EC,
1999/91/EC about materials and articles made
of plastics and intended to come into contact
with foodstuffs or toys and in the "
German Bedarfsgegenstandeverordnung"
of April 10th, 1992 as hereafter including
December 21st, 2000. |
|
|
 |
|
|
Polymer additives intended for anti-drip
benefits are particularly useful in wire and
cable and building material applications.
In granular form, when added to thermoplastic
resins, polymer additives utilize fibrillation
to significantly improve anti-drip properties,
melt strength and sag resistance in applications
like wire and cable insulation and jacketing,
tubes, hoses, pipe liners and housings.
These anti-drip characteristics can help retard
flame propagation should the end-use part
be exposed to extremely high temperatures.
They are classified under UL94 V-0. |
|
|
 |
|
Polycarbonate |
PP(Polypropylene) |
Polyamide |
Polystyrene |
Polystyrene |
PBT (Polyester) |
|
|
|
 |
High molecular weight granular fluoropolymers
with the capacity to fibrillate during melt
blending
processes
Testing shows reduced drip and propagation
of flame (UL94 V-0 qualification)
Added melt strength, sag resistance and viscosity
during processing
Increased die swelling |
|
|
 |
High molecular weight fluoropolymer dispersions
with the capacity to fibrillate during melt
blending
processes
Highly concentrated, fluoropolymer lattices
allowing wet blending with other polymer dispersions
prior
to coagulation |
|
|
|
Properties |
Unit |
Test
method |
PA
5931 |
PA5932 |
PA5933 |
PA5958 |
PA5959 |
Average
Particle size |
§ |
Laser
Diffraction |
500 |
500 |
500 |
0.2 |
0.2 |
Bulk
density |
g
/ l |
ASTM
D 4895 |
510 |
510 |
510 |
- |
- |
Solids
Content |
% |
ISO
12086 |
- |
2 |
2 |
60 |
58 |
|
|